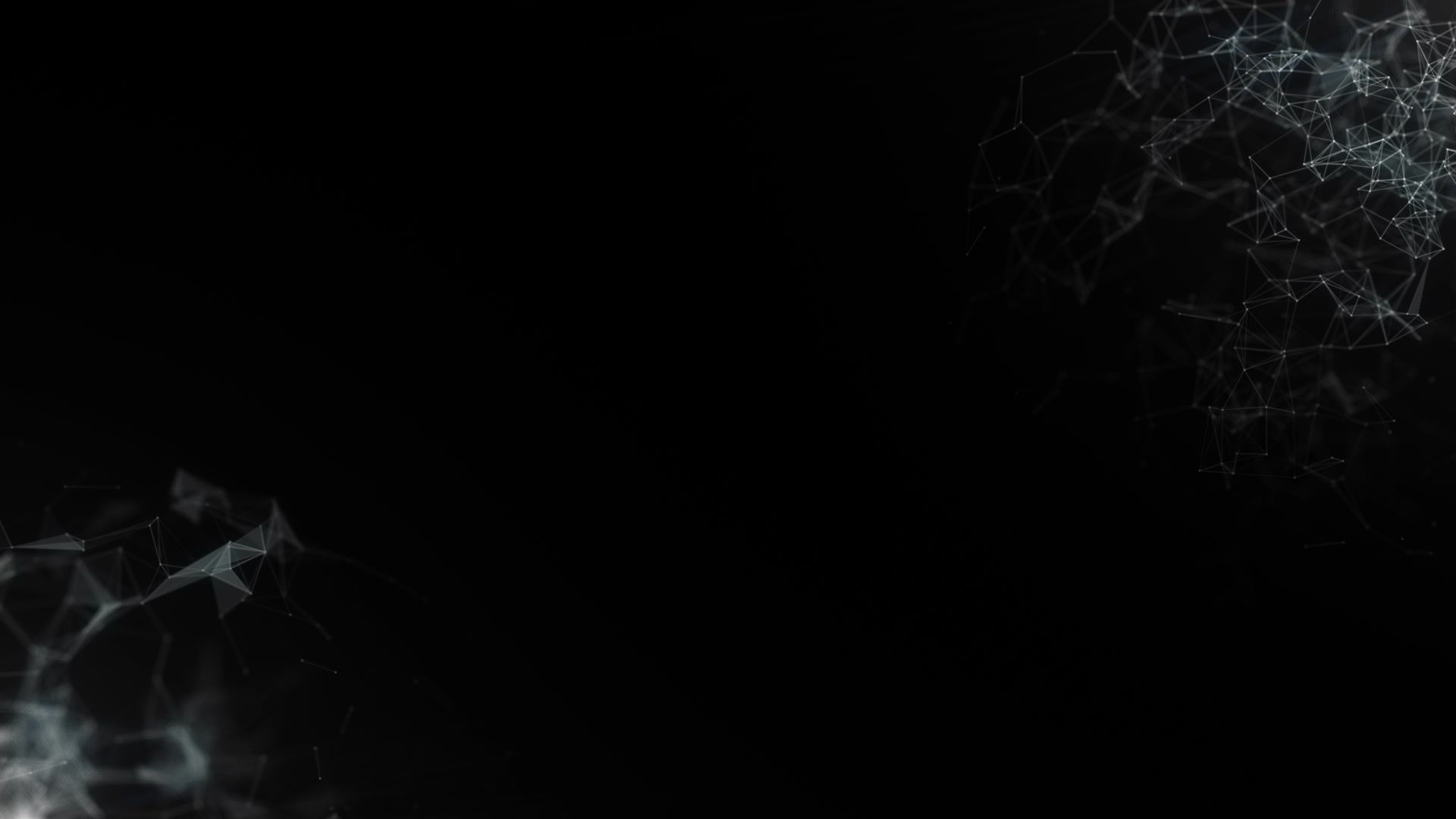
Design Process Checklist - A step-by-step guide
Nobody likes surprises, and nothing during the design and development of your product should be a surprise. Nonetheless, if you're new to product development, there are some things that come as a surprise.
The first "surprise"; time. Not money, but time. Having done design now for 30 years, I have a pretty good idea how long it takes to accomplish a task. A "simple" PCB layout; a couple of days - full "new product" development, depending on what it is, could take a year. How can I be certain I'm right with a time estimation? It's what I base my quote on; if I'm not very close to actual, I can end up working for $5/hour...
Money. Top two, time and money. What can be said about money, other than by following a complete specification and experience to know "what works and what doesn't", all quotes from SCARY Design minimize non-recurring engineering (NRE) so that as much money as possible goes to design for production.
NRE is a topic one wouldn't normally hear from a design group; no one wants to talk about it for this simple reason - spending money on NRE is no different than taking that same amount of money and throwing it in the trash. It's usually used in the same sentence as "R&D" (research and development). If one is not careful, this is the money used to "try something" or "test something", the output of which may (good) or may not (bad) have a direct impact on the production product. NRE is a fact of life; the goal is to minimize these costs. Knowledge and experience can help mitigate these charges. If you're doing a project with a design group, and there's a "lot" of NRE, chances are they're going to be "learning" on your dime.
Over the years, we've developed a "guide" to help everyone stay on the same page, or more to the point, a "clear contract". A "clear contract" is one in which all parties involved are in complete understanding with one another; nothing is left open or assumed.
Before spending a dollar, you should know ahead of time of what to expect from us, what we expect of you, and exactly where we are in the process of taking your idea from concept to finished design.
Listed here are the major steps we take developing your product. Every project is different; some steps might not be appropriate, some steps may be more involved and necessary than others.
Design guide:
Project intro:
A short discussion, usually via phone or TeamViewer in which the initial project is discussed. This is where we'll sign any Non-Disclosure Agreements (NDA) if needed. It's also here where an assessment of the project is made, and whether we're the right design house for you. This is an important point to make; not every "design house" is equal. For example, we're very good at consumer electronics products; typically "form follows function" designs.
Project acceptance/Specification Generation:
If we accept your project, the first step is compiling a "specification". This is where we generate a document by which we'll design. Initially a "thumb nail sketch" of the project is created; we then drill down into the design until we have a "living document" detailing the project.
Electronics/Mechanical Design:
Design work begins on circuit and mechanical design. It's important at this point to work out the mechanical design; this should drive the PCB layouts.
Electronics:
Circuit design and simulation (LTSpice) is begun. Simulation of the electronics is critical at this stage; we want to have as many details of the design as possible detailed and working prior to starting PCB layouts.
Mechanical:
An "enclosure" is either purchased off the shelf or custom designed to suit the project. All mechanical design is completed and 3D model motion tests performed (if applicable).
Mechanical components purchased, 3D models "printed":
All mechanical components are purchased, made in a machine shop and/or 3D printed.
Schematic capture and PCB layout:
Schematic capture (drawing the circuit in electronics CAD) is completed and a PCB design begun.
PCB prototype boards and build:
PCB's are made and a small quantity (usually 10, but can be less) are built up in house. We do the first builds ourselves; this is the first pass at the manufacturability of PCB. We identify any mechanical issues that may be present.
Circuit test, programming and verification:
Testing of the circuit is performed, characterizing the design. Verification of power supplies, noise, circuit programming (if needed) performed.
Prototype build and tested:
The prototype is built and tested. Verification of the system is performed.
Life/focus testing:
The prototype is delivered to the client for verification and testing. All aspects of the prototype are checked against the specification. Testing is performed.
Re-spin:
If any component of the design does not meet expectations, it is modified and updated. Many times these are minor things that do not require re-spin of parts or PCB's. If a re-spin is needed, those components are once again manufactured and the prototype updated.
Design files/turnkey package created:
All design files are created needed to produce the product. This includes all electronics design files; schematic capture in native and PDF formats, PCB files in Gerber format and PDF "proofs" generated, all mechanical 3D models in native format including part and assembly files. Special instructions created for any aspect of the project needing details. Turn-key package delivered to client.